富士フイルムロジスティックス株式会社(以下、富士フイルムロジスティックス)様は、富士フイルムグループの物流を担う会社です。今回UM工程進捗を導入いただいた拠点(東HUBグループ)では、富士フイルムビジネスイノベーション株式会社の複合機・プリンターの流通加工を取り扱い、お客様先に配送する前にオプション品の組込みやお客様固有の設定作業を行っています。
今回、東HUBグループ マネージャーの松下様と、同じく東HUBグループの木原様のお二人に、UM工程進捗の導入と稼働後の効果について伺いました。
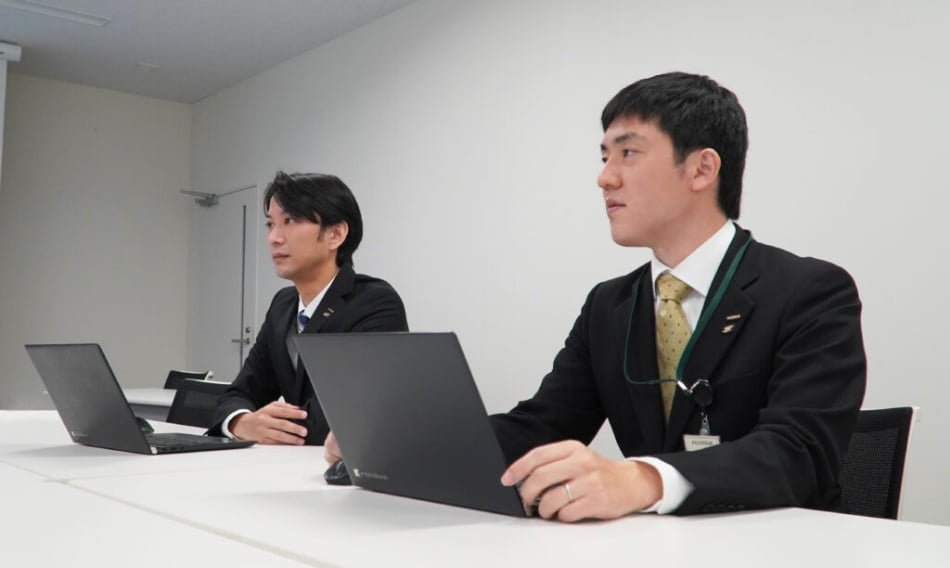
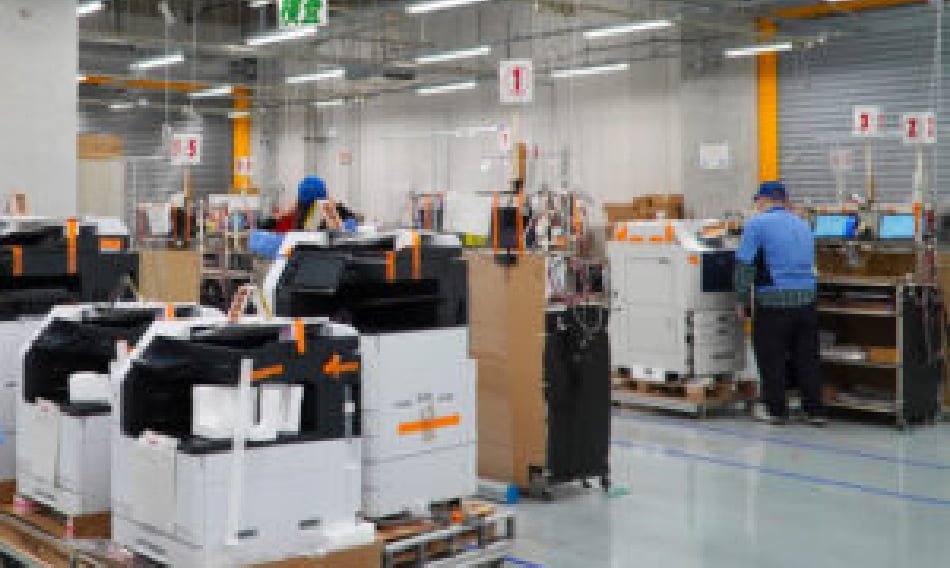
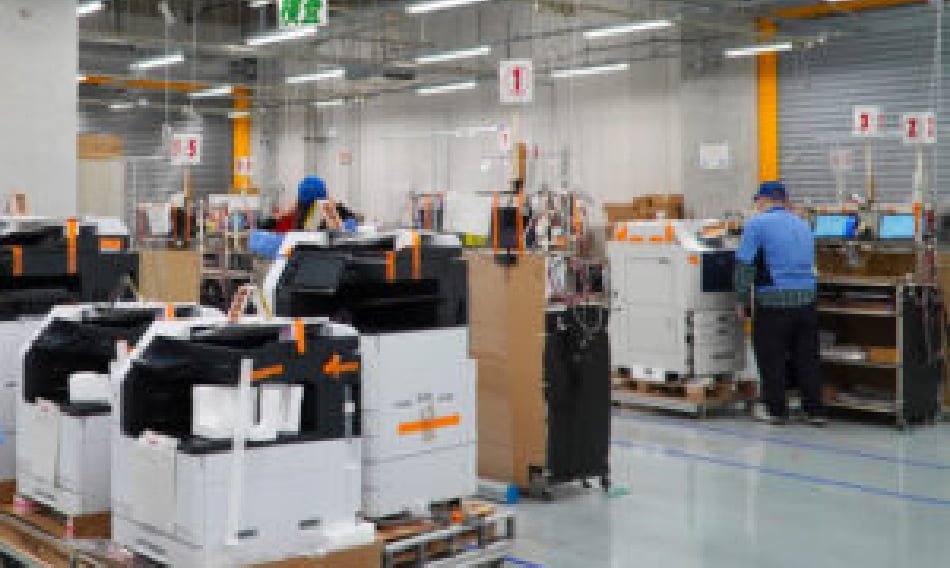
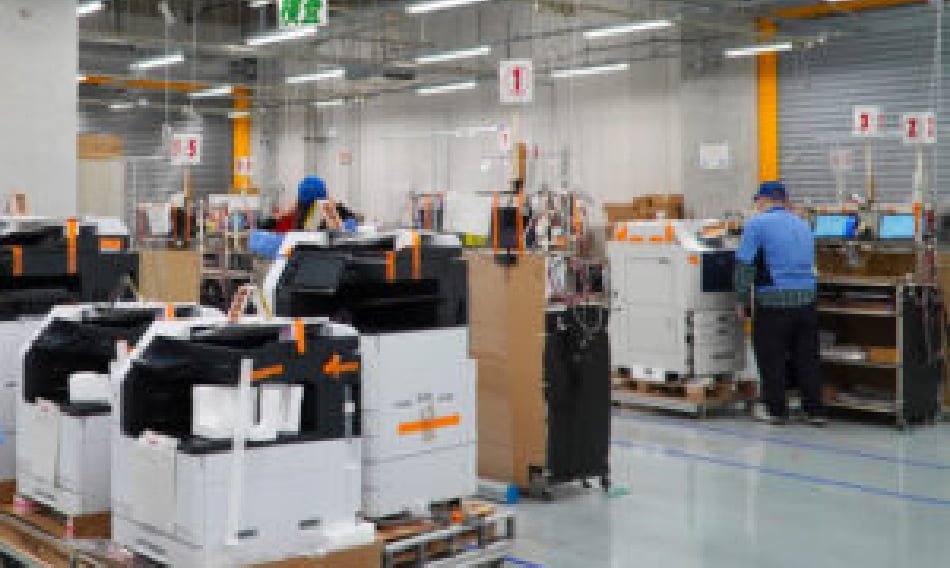
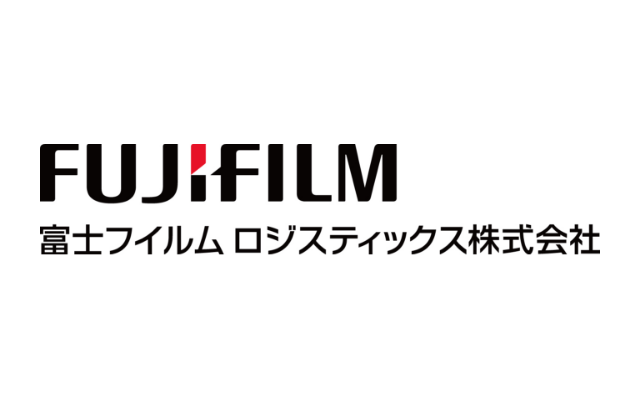
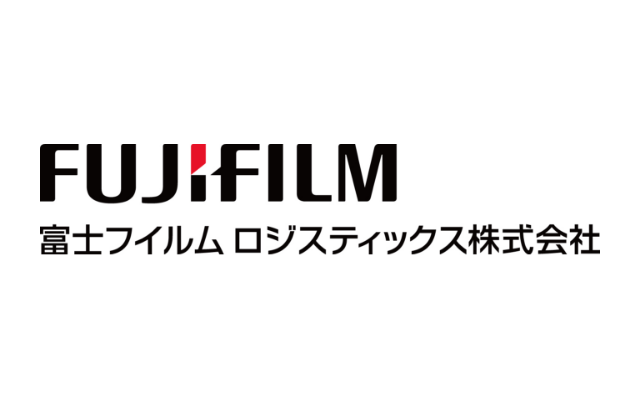
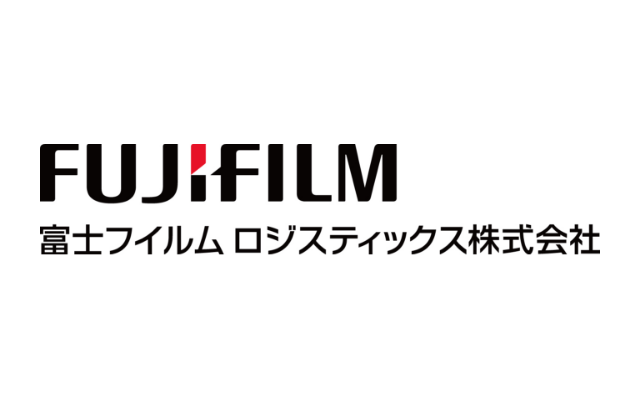
- 富士フイルムロジスティックス様について
- 富士フイルムグループの物流機能会社として幅広い製品・関連部材の物流設計から輸送を行っている
- 富士フイルムロジスティックス様
- お話をお伺いした方
- 東HUBグループ マネージャー 松下様
東HUBグループ 木原様
- ご利用モジュール
- UM工程進捗
※ この事例に記述した数字・事実はすべて、事例取材当時に発表されていた内容に基づきます。数字の一部は概数、およその数で記述している場合がございます。
作業時間をデータとして取得、紙を削減したい
システム導入を検討し始めたきっかけは何ですか?
当拠点では、富士フイルムビジネスイノベーション株式会社と協力会社様と、三者一体となっての業務改善を推進しています。その一環として、作業時間をデータとして取得したいというテーマが挙がりました。そして、データ取得をするためにシステムを検討するのであれば、併せて何か他の改善にもつなげられないかと考えたところ、作業指示書の紙出力を削減しよう、という案が出ました。これが、今回UM SaaS Cloudを導入することになった直接のきっかけです。
導入前は、作業指示書として年間約80万枚紙を出力
導入前はどのような課題をお持ちでしたか?
各工程ごとの作業時間をデータとして取得したいというのがかねてからのテーマでした。ストップウォッチなども試してみたのですが、測定者を置くといった、作業時間を測るためだけの工数が必要なのがネックでした。
もう一点、作業指示書の方ですが、以前は年間で約80万枚を紙で出力していました。当然、その分だけコストがかかるので、何とかこれを削減できないかと悩んでいました。
また、出力した作業指示書は作業後にスキャンしてデータ保存していましたが、文字データではなく画像データなので、活用範囲が限られていました。
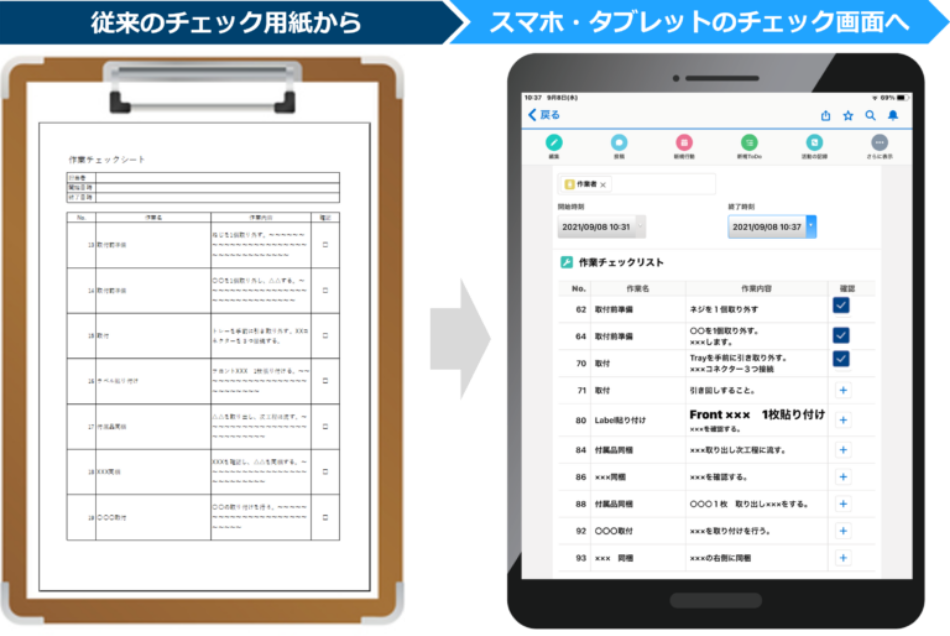
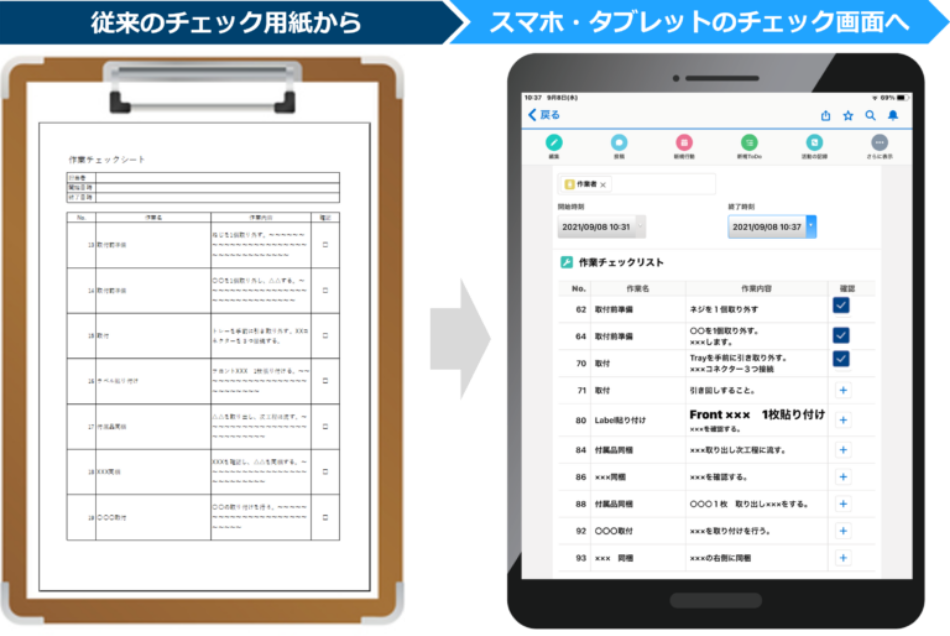
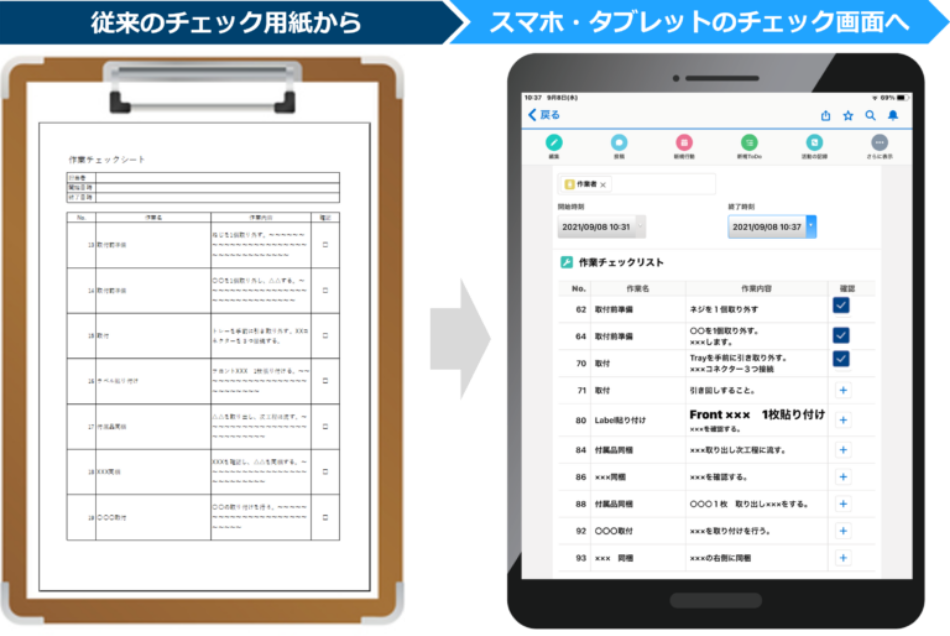
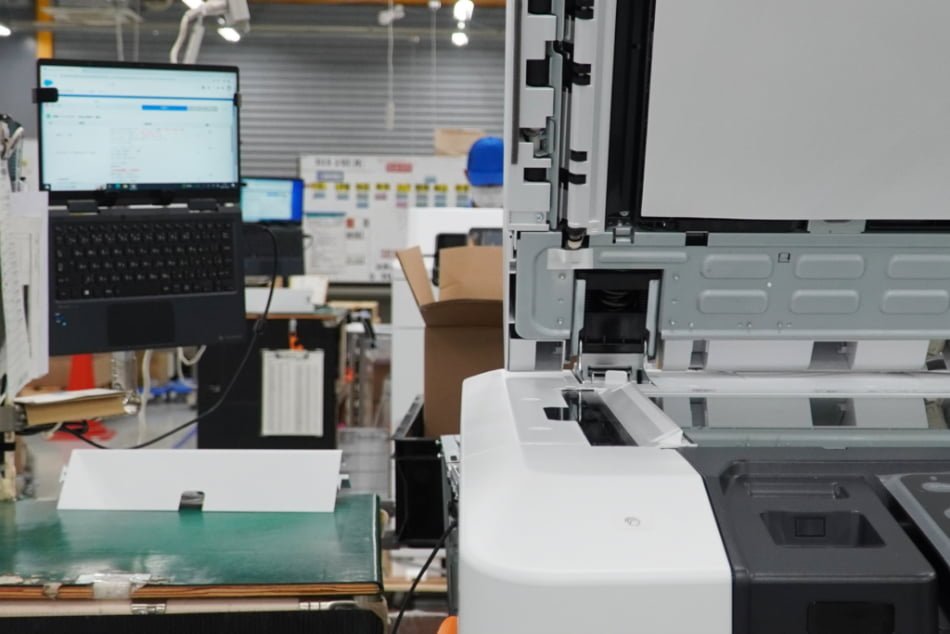
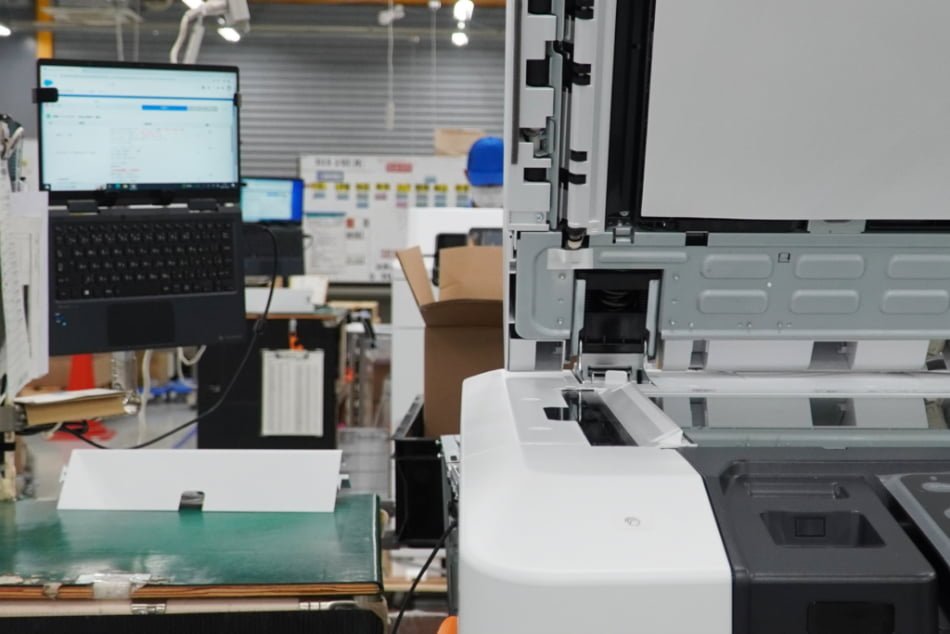
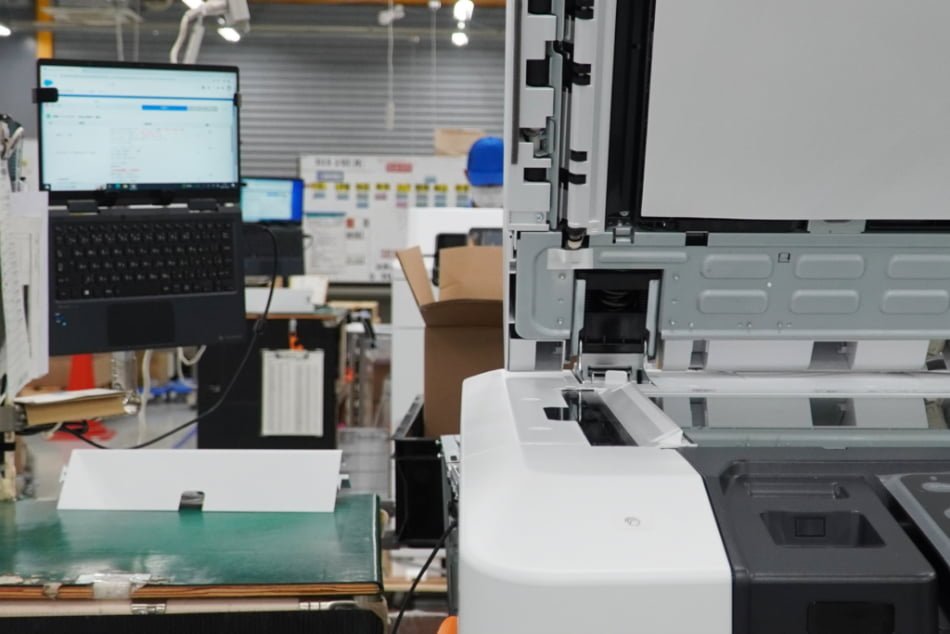
UM工程進捗は、自分たちがやりたかったことがそのまま実現できる!
UM SaaS Cloudを選んだ決め手を教えてください
最初はグループ会社が使っていた、帳票を電子化するツールを検討しました。グループ会社の現場に足を運んでヒアリングし、システム担当者と相談を重ねました。その結果、自分たちがやりたいこととマッチしない、導入や保守の工数がかなりかかりそうということで候補から外しました。その会社は3名ほど専属のシステム担当を立てているとのことで、そこまでの工数は捻出できないと感じましたね。
その後、別のサービスはないか調査したところUM工程進捗の製品ページを見つけ問い合わせしました。
デモを見せてもらったときに、「自分たちがやりたかったことがそのまま実現できる!」と思い、すぐに導入を決断しました。
一番の決め手は紙の指示書のフォームをそのままPC画面に表示する事が出来たことです。また、工程ごとの作業時間のデータが取れる事も導入を決めたポイントでした。作業指示とそのチェックが簡単にできる点も使いやすそうだと感じました。他にも、キーボードやマウスではなく、スマホのようにタップで操作ができるというのもポイントでした。これまで紙を使っていた作業者の方たちにとって、急にシステムを入れるのは抵抗感がありそうなので、スマホを使える人であればそれと同じ感覚で使えるように、ということを意識したとき、UM工程進捗ならスムーズに導入できると考えました。
工程ごとの作業時間を取得でき、現場の状況を数字で可視化
導入後、どのような変化がありましたか?
まず、期待通りに工程ごとの作業時間がデータで見えるようになりました。1つの複合機の作業開始から作業終了するまでの時間しか見えていなかったのが、その間に発生する工程それぞれにかかる作業時間を取得できるようになりました。以前は現場の進捗状況を人間の目で見て、遅れている工程があれば応援の投入をするといった判断をしていたのですが、今は進捗を数字データで見られるので、判断がスムーズになりました。データをベースに、工程ごとの作業時間の差を分析できるようにもなりました。
また、ペーパーレスを実現する事が出来ました。当拠点での作業は複合機1台ごとにやるべきことが異なるので、以前は1台ごとに10枚ほど指示書を印刷していたのですが、今はUM工程進捗上でボタンをクリックするだけで個別の作業指示を出せるので、紙や印刷待ちの時間が削減できましたし、事務の担当者も楽になったのではないかと思います。
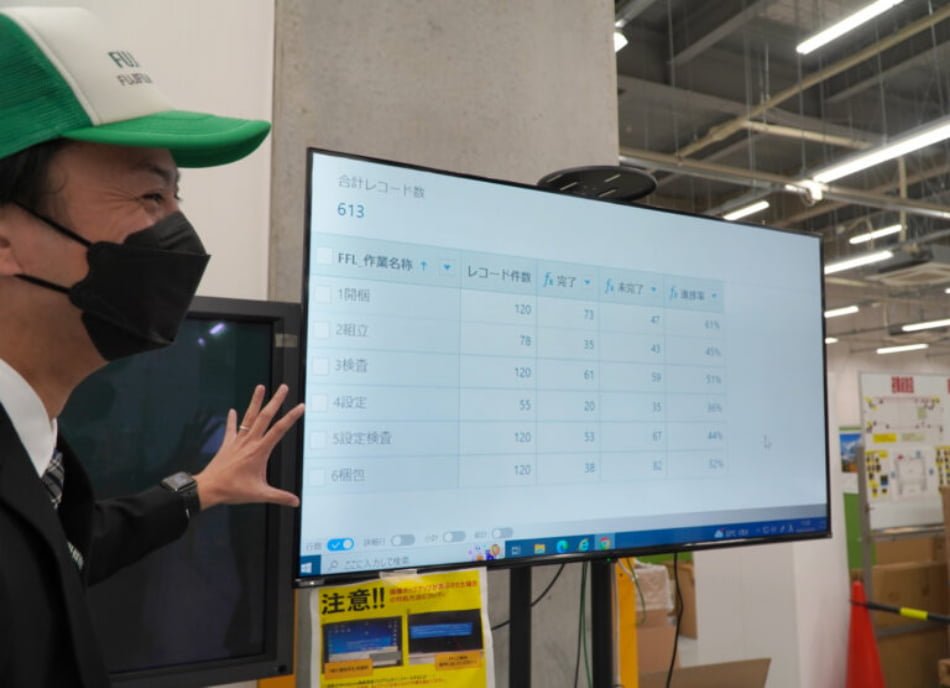
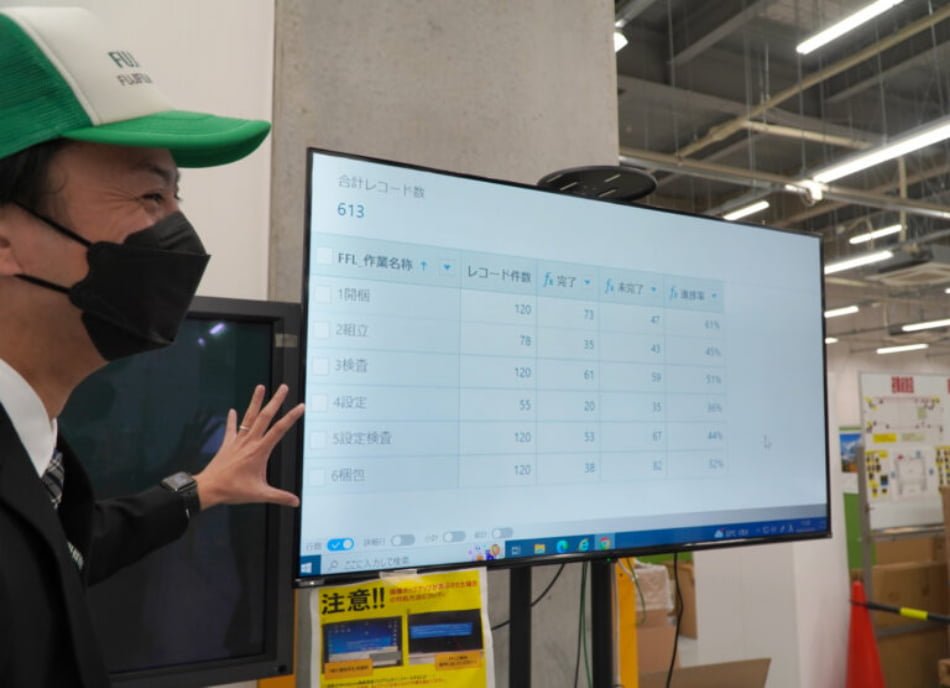
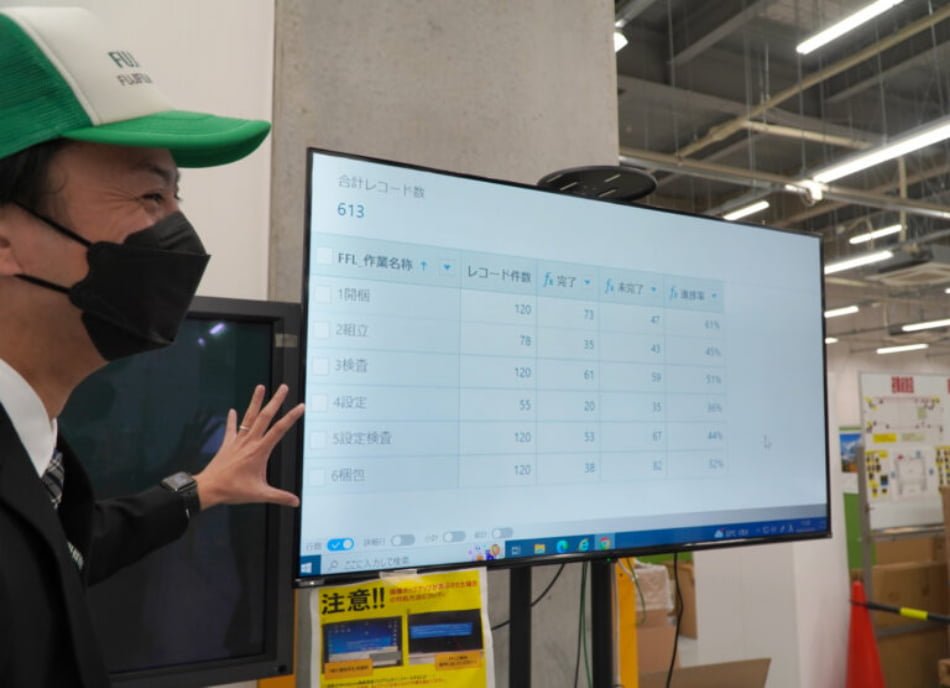
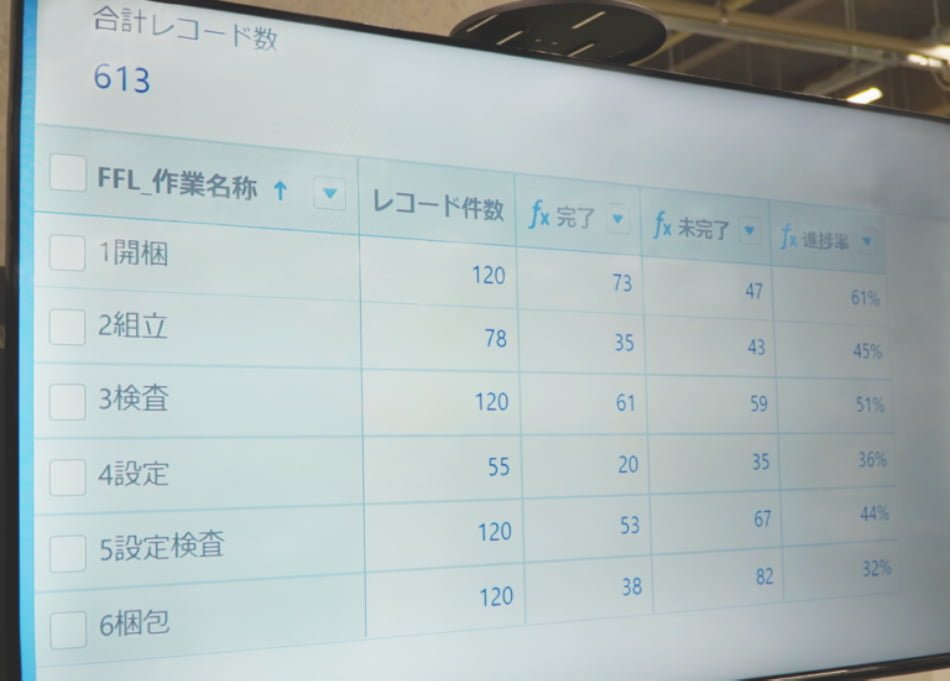
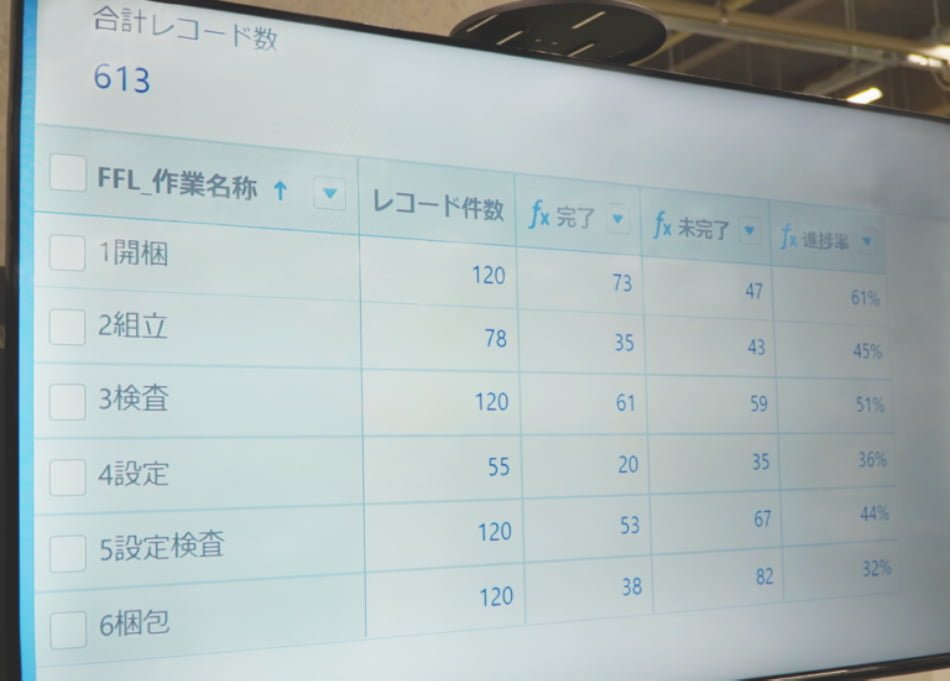
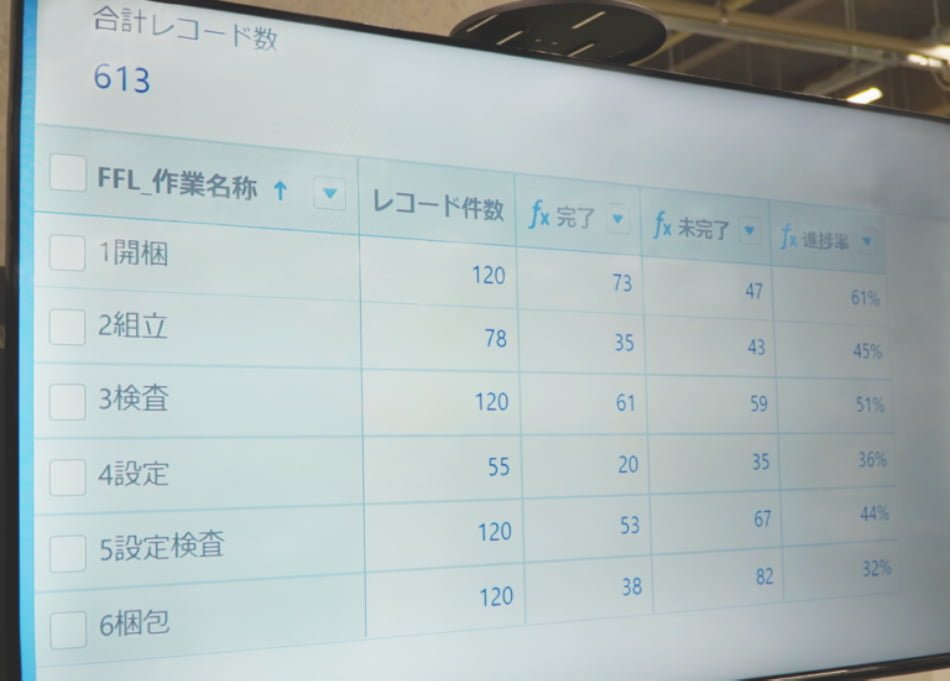
タッチパネル式のPCを採用、PCに不慣れな作業者の抵抗感を減らすことに成功
導入中・導入後に工夫したことや感じたことがあれば教えてください
作業者にとってのギャップをできるだけ減らす工夫として、システム上の作業指示画面を、もともと使っていた紙の指示書と近いフォーマットにしてもらいました。選定時のポイントとして、スマホが使える人であれば使いこなせるようにというものがあったので、タッチパネル式のPCに作業指示を表示して、作業が完了したらタップ1つでチェックを付けられるようにしています。文字を記録しなければいけない箇所もありますが、これも基本的にはバーコードを読み込むだけで入力が完了するようにしています。また、以前は目視で行っていた加工対象の複合機本体と外装箱に記載されたシリアルナンバーの照合もバーコード読み取りによりUM工程進捗の画面で照合結果を確認できるようになり、作業者の負担を軽減しました。
もともとは追加開発なしの標準製品のまま使えると考えていたのですが、結果的に、後から「こんなこともしたい」と要望を追加させてもらうことになりました。それにも関わらず、スムーズに開発していただき、オンスケジュールで導入が完了したことが記憶に残っています。システム導入はスケジュールの遅延が多いイメージだったので、予想外のスピードで進んだと感じています。
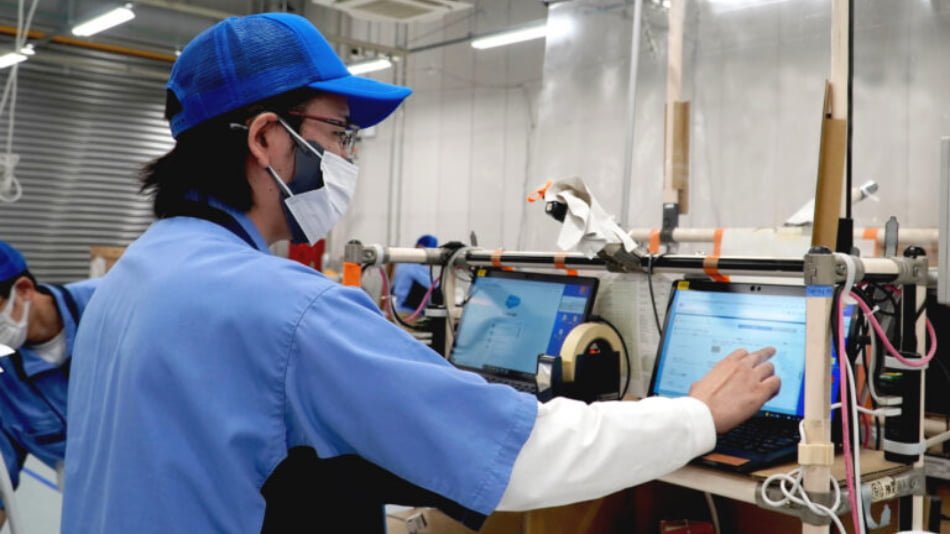
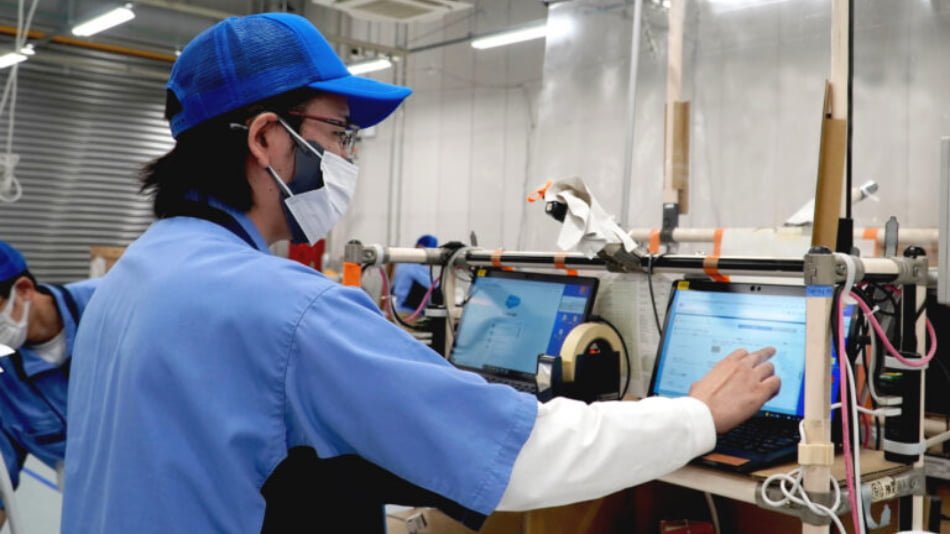
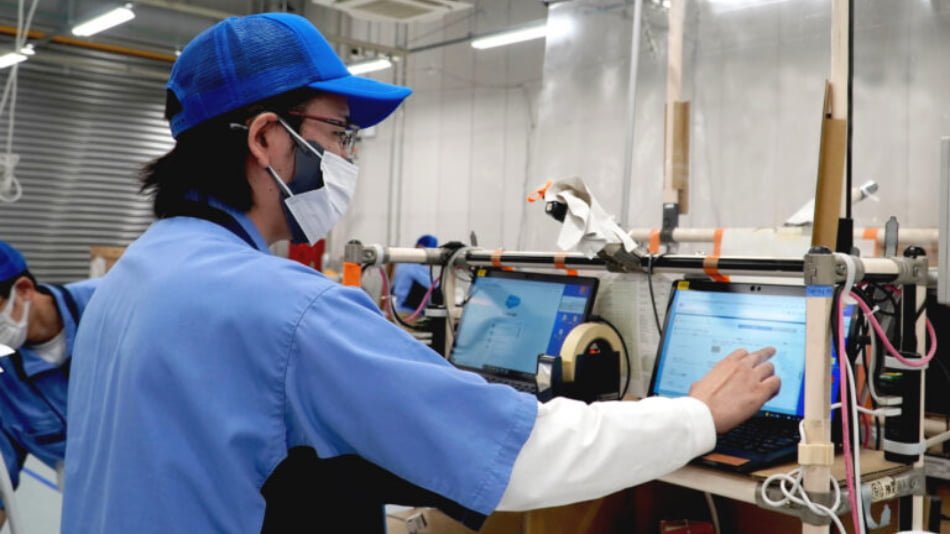
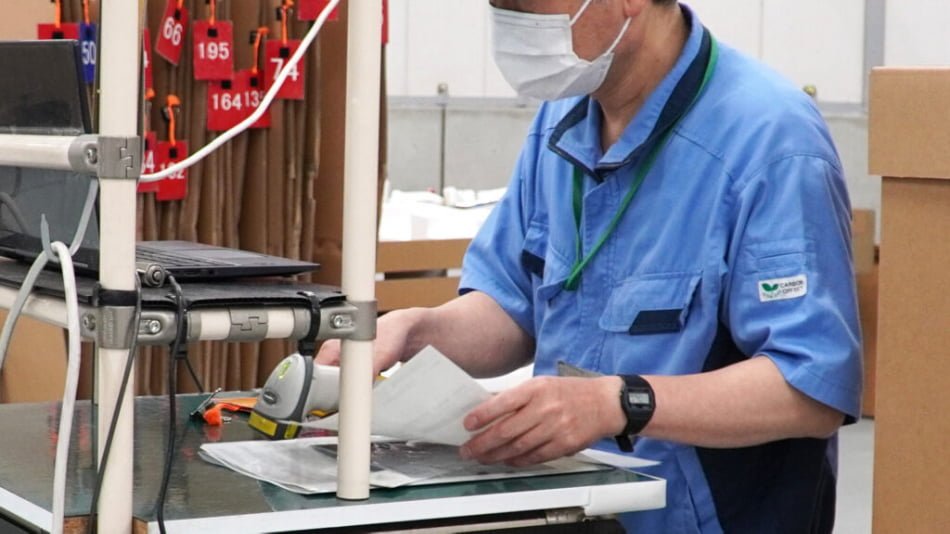
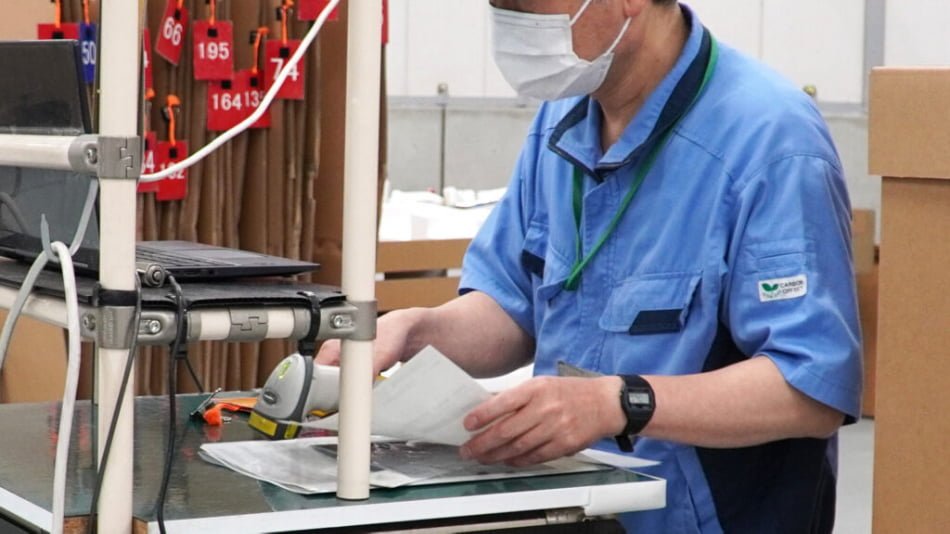
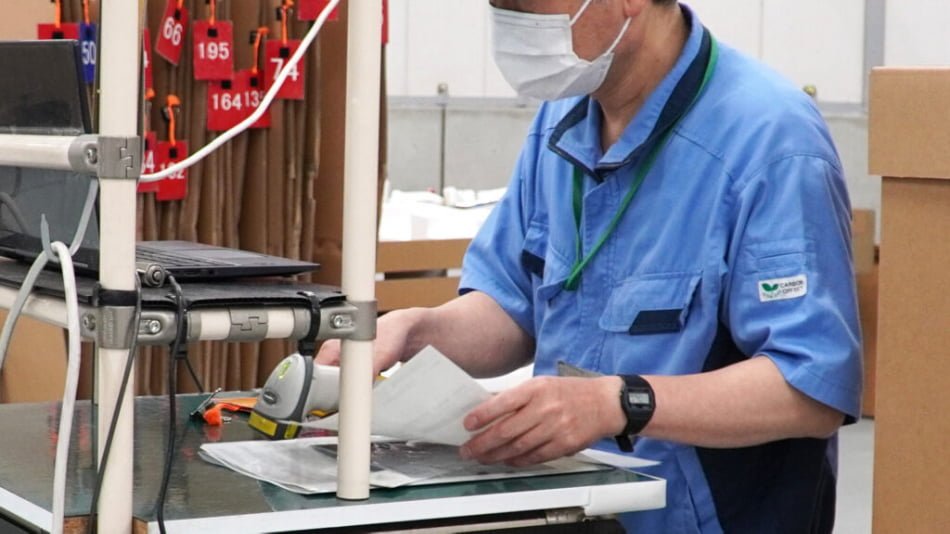
他拠点へ展開し、拠点間での違いを分析
UM工程進捗の活用について、今後の展望をお聞かせください
今回の導入が完了し、スムーズに稼働しているので、次は他拠点への展開を予定しています。同じシステムを使うことで、拠点間でどういった違いがあるか比較もできるのではと期待しています。比較、分析を重ねて、さらなる改善につなげていきたいです。